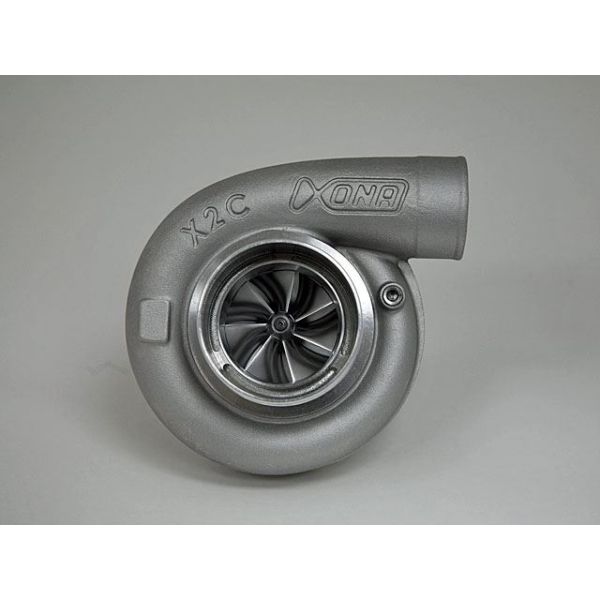
Xona XR 6157S X2C .63ar TiAL vBand Ball Bearing Turbo

Found it for less but value our service?

Details
Xona XR 6157S X2C .63ar TiAL vBand Ball Bearing Turbo
Quick Specs:
Compressor Wheel: 55/76mm
Turbine Wheel: 64/57mm UHF Technology
HP: 320-640
Max Compressor Flow: 61lb/min
Product Details
Xona Rotor has implemented innovative features in its XR line of performance turbochargers to enhance performance and durability. Among them is Xona’s proprietary variable-preload ball bearing cartridge system. Traditional bearing systems with insufficient preload can experience ball sliding and scuffing at high shaft speeds, leading to fretting of the bearing races and short bearing life.
The bearing housing itself is a fully-machined, high-strength stainless steel component with an extended water jacket. By fully surrounding the turbine seal ring land area, this advanced cooling feature combats heat soakback, preventing piston ring collapse for enhanced durability at high temperatures.
A turbocharger’s bearing system is its heart, and Xona Rotor has left nothing on the table. Xona XR turbochargers use hybrid (ceramic balls and steel races) ball bearing cartridges unlike those found elsewhere. These high-precision ABEC 7 angular contact ball bearings are made with advanced M62 high-speed powder metal steel races, silicon nitride ceramic balls and metallic ball cages. No melted ball cages here. Together these features deliver significantly elevated robustness and durability at extreme temperatures compared to conventional ball bearing systems.
Most performance turbochargers today use a single piston ring for sealing the shaft at each end. By contrast, Xona XR turbochargers employ twin rings at both the compressor and turbine ends. This feature dramatically reduces oil leakage and gas intrusion at both ends of the rotating assembly. Furthermore, since the sealing load is spread across two rings, wear rates are reduced and seal life is extended. Complementing this are large-diameter oil slingers incorporated into both ends of the shaft, further reducing splash oil at the piston ring seal location within the bearing cartridge.
The compressor register of the CHRA features an overbuilt compressor backplate and cover interface system that is very tolerant of external loads, limiting structural distortion that can lead to compressor wheel rubbing and premature failure.
At the oil inlet, XR turbochargers offer a choice of 7/16" inverted flare or straight M12x1.25 connections. Built into the oil inlet cavity of the CHRA is a large volume “last ditch” oil filter element that prevents oil contaminants from entering the bearing system and plugging oil passages within the turbocharger. At the other end of the Xona XR’s bearing housing, a modular oil drain flange allows for a variety of bolt spacing.
UHF Turbine Wheel *Next-Generation Turbine Aero
Xona Rotor’s second-generation turbine wheel has arrived. Known as UHF (Ultra High Flow), its mission was to maximize flow capacity and raise efficiency.
UHF is Xona Rotor’s most advanced wheel yet. Among other details, UHF’s patent pending splitter-blade design allowed the blade loading to be fine-tuned in order to achieve its performance objectives.
Turbine design is a multi-variable juggling act. One feature that heavily influences a turbine’s mass flow “swallowing capacity” is the throat region located near the exit of the wheel. An effective method to increase the throat area is to decrease the number of blades. While reducing blade count tends to increase the turbine’s flow capacity, efficiency typically suffers.
Introducing splitter blades provides an elegant solution to the trade-off between flow and efficiency. The splitter blades alleviate the blockage in the throat area while preserving the fluid momentum at the wheel inlet.
The result is that UHF has the swallowing capacity of a low blade-count turbine with the efficiency of a high blade-count configuration. Its improvements were observed analytically, validated experimentally on a gas stand and then confirmed in on-vehicle testing.
Why Flow Capacity Matters
So why all this effort to maximize the turbine’s flow capacity? For a given engine operating point – say, full boost near redline – a higher-flowing turbine operates at reduced expansion ratio than a lower-flowing turbine. The lower expansion ratio translates directly to reduced exhaust manifold pressure (“EMAP”).
Lower EMAP means more engine power – the engine’s pumping work is reduced and volumetric efficiency improves. If the engine’s valve events (i.e., overlap) and ignition timing are modified to take advantage of the reduction in EMAP, further gains can be reaped. In the bargain, with reduced EMAP, the engine becomes less knock-sensitive and less prone to overheating.
More Information
Part Number | 12110, 006872 |
---|---|
Brand | Xona |
Type of Part | Xona XR 6157S (640HP) |
Length | 12.0 |
Width | 12.0 |
Height | 12.0 |
Weight | 25.000000 |
Reviews
Fitment
Xona XR 6157S X2C .63ar TiAL vBand Ball Bearing Turbo
Quick Specs:
Compressor Wheel: 55/76mm
Turbine Wheel: 64/57mm UHF Technology
HP: 320-640
Max Compressor Flow: 61lb/min
Product Details
Xona Rotor has implemented innovative features in its XR line of performance turbochargers to enhance performance and durability. Among them is Xona’s proprietary variable-preload ball bearing cartridge system. Traditional bearing systems with insufficient preload can experience ball sliding and scuffing at high shaft speeds, leading to fretting of the bearing races and short bearing life.
The bearing housing itself is a fully-machined, high-strength stainless steel component with an extended water jacket. By fully surrounding the turbine seal ring land area, this advanced cooling feature combats heat soakback, preventing piston ring collapse for enhanced durability at high temperatures.
A turbocharger’s bearing system is its heart, and Xona Rotor has left nothing on the table. Xona XR turbochargers use hybrid (ceramic balls and steel races) ball bearing cartridges unlike those found elsewhere. These high-precision ABEC 7 angular contact ball bearings are made with advanced M62 high-speed powder metal steel races, silicon nitride ceramic balls and metallic ball cages. No melted ball cages here. Together these features deliver significantly elevated robustness and durability at extreme temperatures compared to conventional ball bearing systems.
Most performance turbochargers today use a single piston ring for sealing the shaft at each end. By contrast, Xona XR turbochargers employ twin rings at both the compressor and turbine ends. This feature dramatically reduces oil leakage and gas intrusion at both ends of the rotating assembly. Furthermore, since the sealing load is spread across two rings, wear rates are reduced and seal life is extended. Complementing this are large-diameter oil slingers incorporated into both ends of the shaft, further reducing splash oil at the piston ring seal location within the bearing cartridge.
The compressor register of the CHRA features an overbuilt compressor backplate and cover interface system that is very tolerant of external loads, limiting structural distortion that can lead to compressor wheel rubbing and premature failure.
At the oil inlet, XR turbochargers offer a choice of 7/16" inverted flare or straight M12x1.25 connections. Built into the oil inlet cavity of the CHRA is a large volume “last ditch” oil filter element that prevents oil contaminants from entering the bearing system and plugging oil passages within the turbocharger. At the other end of the Xona XR’s bearing housing, a modular oil drain flange allows for a variety of bolt spacing.
UHF Turbine Wheel *Next-Generation Turbine Aero
Xona Rotor’s second-generation turbine wheel has arrived. Known as UHF (Ultra High Flow), its mission was to maximize flow capacity and raise efficiency.
UHF is Xona Rotor’s most advanced wheel yet. Among other details, UHF’s patent pending splitter-blade design allowed the blade loading to be fine-tuned in order to achieve its performance objectives.
Turbine design is a multi-variable juggling act. One feature that heavily influences a turbine’s mass flow “swallowing capacity” is the throat region located near the exit of the wheel. An effective method to increase the throat area is to decrease the number of blades. While reducing blade count tends to increase the turbine’s flow capacity, efficiency typically suffers.
Introducing splitter blades provides an elegant solution to the trade-off between flow and efficiency. The splitter blades alleviate the blockage in the throat area while preserving the fluid momentum at the wheel inlet.
The result is that UHF has the swallowing capacity of a low blade-count turbine with the efficiency of a high blade-count configuration. Its improvements were observed analytically, validated experimentally on a gas stand and then confirmed in on-vehicle testing.
Why Flow Capacity Matters
So why all this effort to maximize the turbine’s flow capacity? For a given engine operating point – say, full boost near redline – a higher-flowing turbine operates at reduced expansion ratio than a lower-flowing turbine. The lower expansion ratio translates directly to reduced exhaust manifold pressure (“EMAP”).
Lower EMAP means more engine power – the engine’s pumping work is reduced and volumetric efficiency improves. If the engine’s valve events (i.e., overlap) and ignition timing are modified to take advantage of the reduction in EMAP, further gains can be reaped. In the bargain, with reduced EMAP, the engine becomes less knock-sensitive and less prone to overheating.